目次
日本が誇る一大自動車生産メーカーとして、世界のモノづくりを牽引するトヨタ自動車。そのトヨタ自動車を含むトヨタグループの歴史や技術が学べる記念館が、愛知県名古屋市の「トヨタ産業技術記念館」です。
記念館というと少し固いイメージがありますが、同施設は子どもから大人まで幅広く楽しめる博物館として大好評なんです!その人気ぶりは、トリップアドバイザーが選ぶ「旅好きが選ぶ!工場見学&社会科見学ランキング」で、4年連続1位を獲得するほど。近年は海外からも多くの人々が訪れています。世界中の人を惹きつける、トヨタ産業技術記念館の魅力に迫ります。
後編では、トヨタの自動車づくりをさまざまな角度から学べる「自動車館」を中心にご紹介していきます。
▼前編の記事はこちら
トヨタの自動車づくりをさまざまな角度から紹介
「自動車館」
延べ7,900㎡の広さをほこる自動車館では、トヨタの自動車づくりをさまざまな角度から紹介しています。豊田佐吉の長男である豊田喜一郎が中心となり、国産自動車の生産をはじめるまでの足跡から、創業期から現代にいたるまでの歴史や技術の進歩を知ることができます。
世界のモノづくりを牽引するトヨタ自動車の世界をのぞいてみましょう。
繊維機械から自動車へ
なぜ繊維機械を主としていたトヨタグループが、自動車事業に着手したのでしょうか。
そのきっかけとなったのは、豊田喜一郎が1921(大正10)年に訪れた欧米の紡織業視察です。喜一郎は、すでに大衆の足となりつつあった自動車の発達に目を奪われました。もう一つのきっかけは、1923(大正12)年に発生した関東大震災。当時の日本の物流の中心であった鉄道網は破壊され、輸入トラックや、T型フォードを改良した「円太郎バス」が復興の足として大活躍しました。
円太郎バス
震災後、自動車の普及がはじまった日本ですが、1925(大正14)年にはフォード社。1927(昭和2)年にはGM社と、米国メーカーが日本国内に工場を設け、生産台数がどんどんと増えていきました。そのため、日本の自動車市場は約99%が外国車という状態だったのです。
トヨタグループ創業者である豊田佐吉の長男・豊田喜一郎
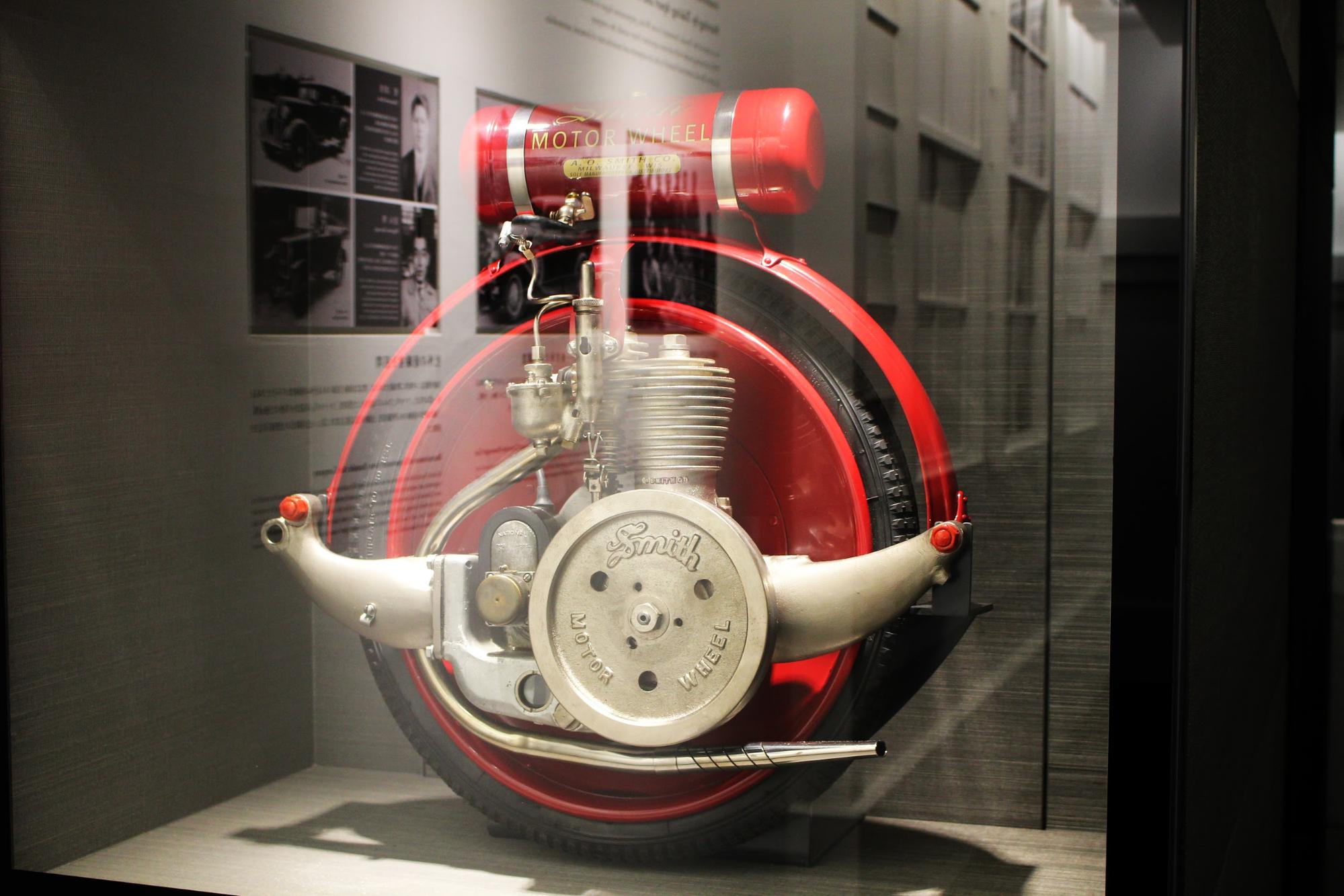
スミス・モーター・ホイール
「これからは自動車の時代だ!」日本人の頭と腕による国産自動車をつくろうと、豊田喜一郎は、若い技術者たちとともに自動車の研究に踏み出します。自転車に取り付けて使用する小型エンジン「スミス・モーター・ホイール」を参考に、小型ガソリンエンジンの試作からスタートしました。
自動車事業への進出には莫大な資金が必要なことから、社内外からは強い反対意見がありました……。しかし、喜一郎は豊田利三郎社長を説得し、1933(昭和8)年に自動車部を開設。本格的な自動車試作がはじまります。
ゼロから始めた自動車づくり
材料試験室の建設
「材料試験室」実際の建物の一部を移築し、当時の試験室を再現しています。
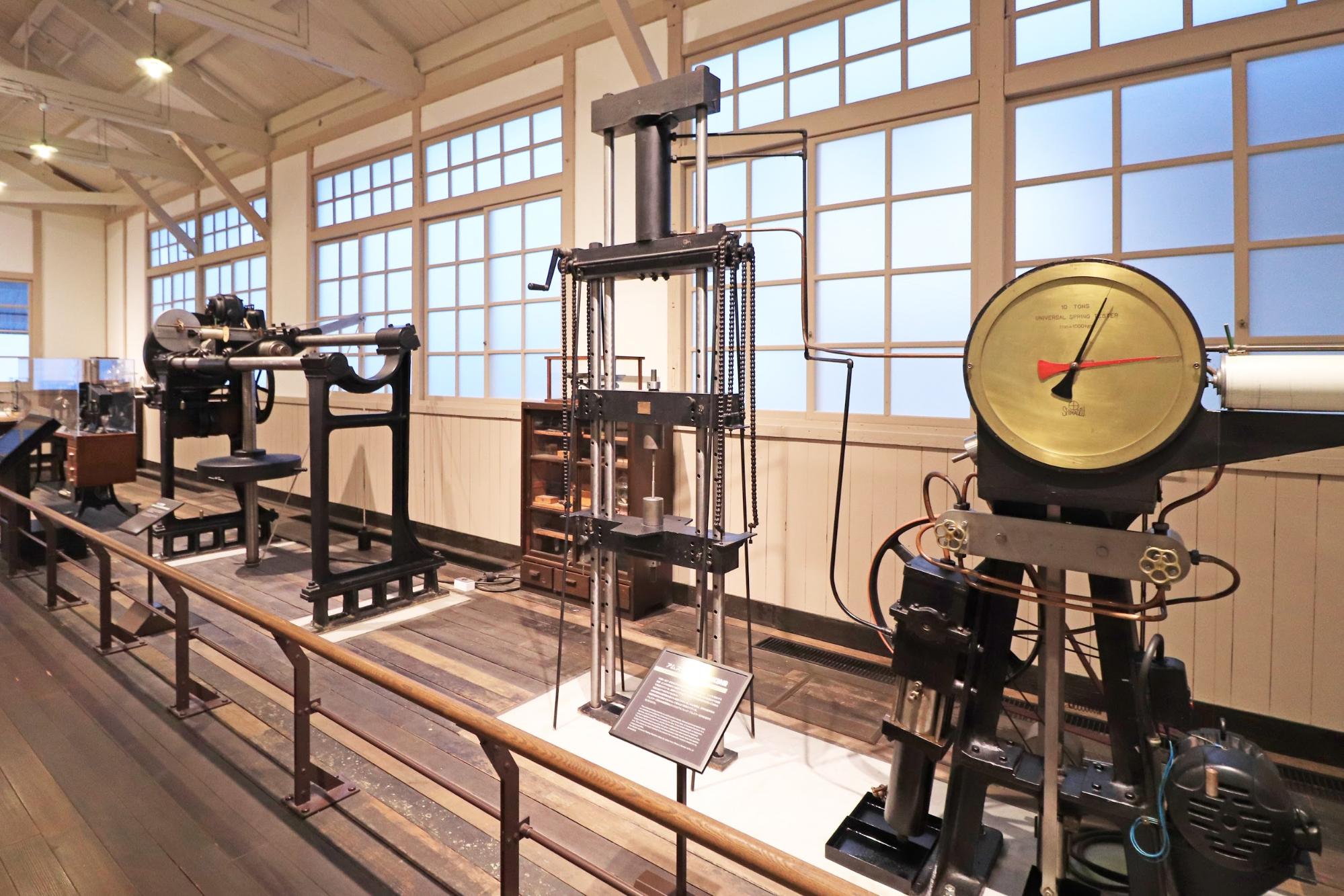
実際に使われていた実験機が、当時に近い形で配置されています。
自動車生産において、最初の課題は「材料の確保」でした。
当時の日本の製鋼業界には、自動車用鉄鋼材料を安定して供給できる能力はありませんでした。そのため、喜一郎は大量生産を見据えた自動車用鉄鋼材料を自前で研究する必要があると判断。当時の帝国大学とほぼ同等の最新研究機器を備えた「材料試験室」を設立しました。
苦闘するエンジン試作
鋳造(ちゅうぞう)の様子
エンジン開発に着手した喜一郎は、まずは自動車の心臓ともいえるエンジンの「シリンダーブロック」の試作に挑みます。シリンダーブロックは、砂でできた型に鉄を流し込み、冷えて固まったあと、砂型を壊して製品を取り出す「鋳造(ちゅうぞう)」という加工法でつくります。
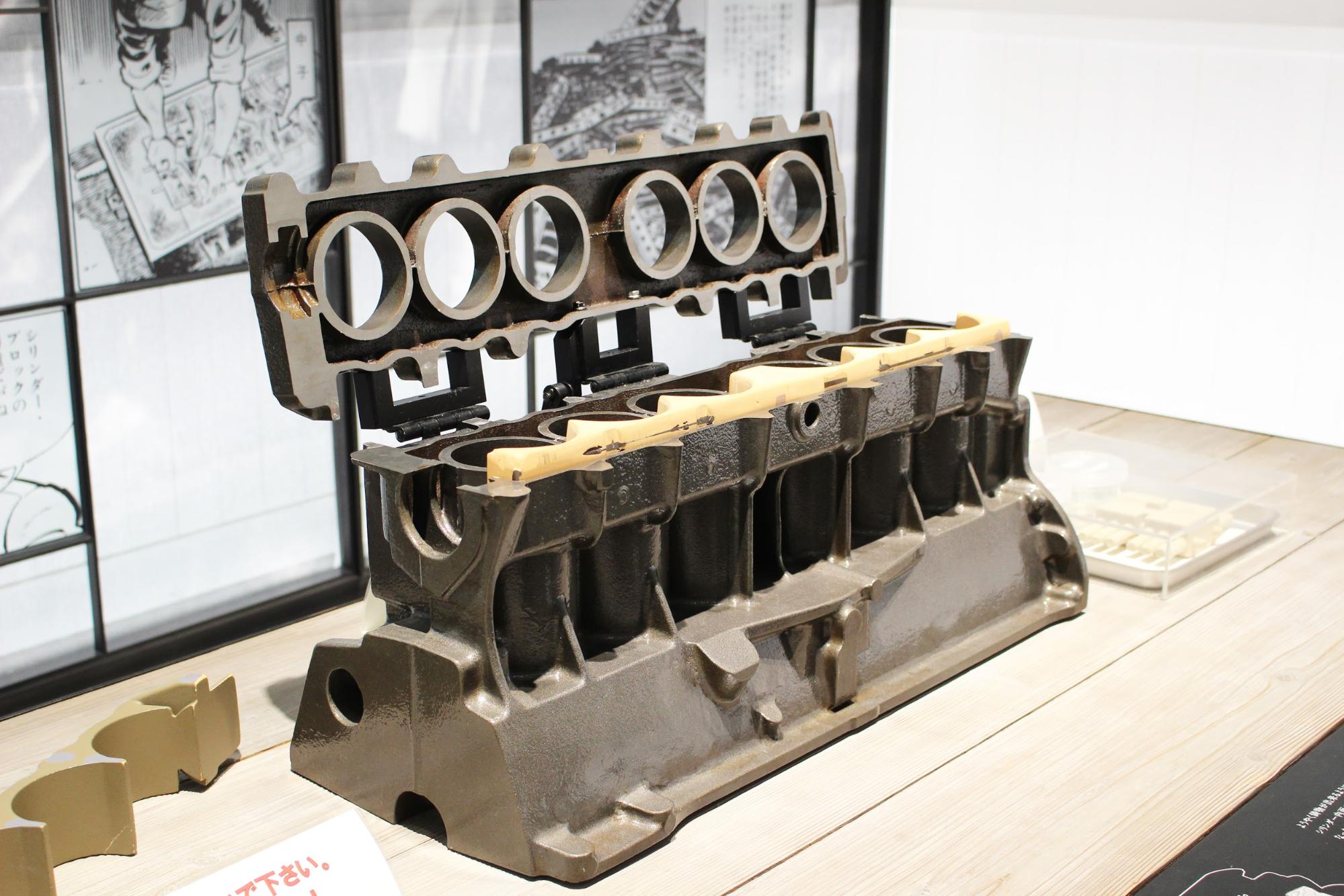
A型エンジンのシリンダーブロック(複製)
紡織機で培った鋳造技術に自信を持っていた喜一郎と仲間たち。ですが、複雑な形状と薄物の鋳物だったため、彼らの持つ従来のノウハウでは製作することができませんでした。試作成功までの3カ月間に、500〜600個のシリンダーブロックが無駄になったそうだ。
こうした悪戦苦闘の日々を乗り越え、「A型エンジン」と名付けられたトヨタ初の量産型エンジンが誕生しました。
流線型とオールスチールボデー
再現された試作工場
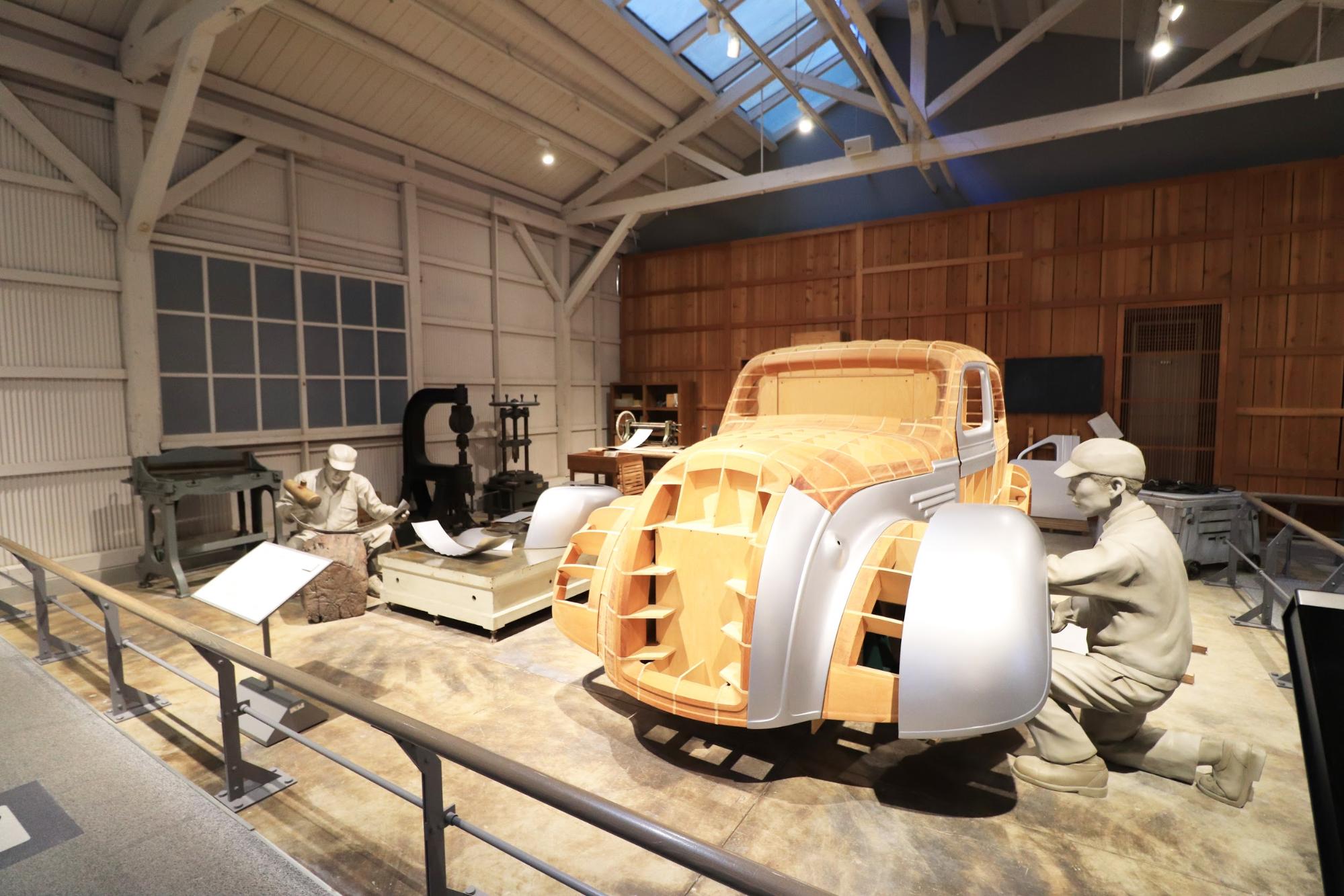
「A1型試作乗用車」のボデーパネルは、すべて手叩きによる板金作業でつくられました。
エンジンの次はいよいよボデーです。
当時の車両の骨格は、木造が主流でした。また、流線型のデザインもアメリカでも最先端のものでした。時代を先取りした永続性のあるスタイルが必要と考え、流線型のデザインとオールスチール製のボデー構造が採用されました。
こうして、自動車部を開設してから1年半後の1935(昭和10)年5月。ようやく最初の試作車「A1型試作乗用車」が完成しました。
アフターサービスの原点にもつながる
「G1型トラックの誕生」
試作工場の先、エスカレーターを上がったコーナーでは、現在のアフターサービスの原点にもつながる「G1型トラックの誕生」が紹介されています。
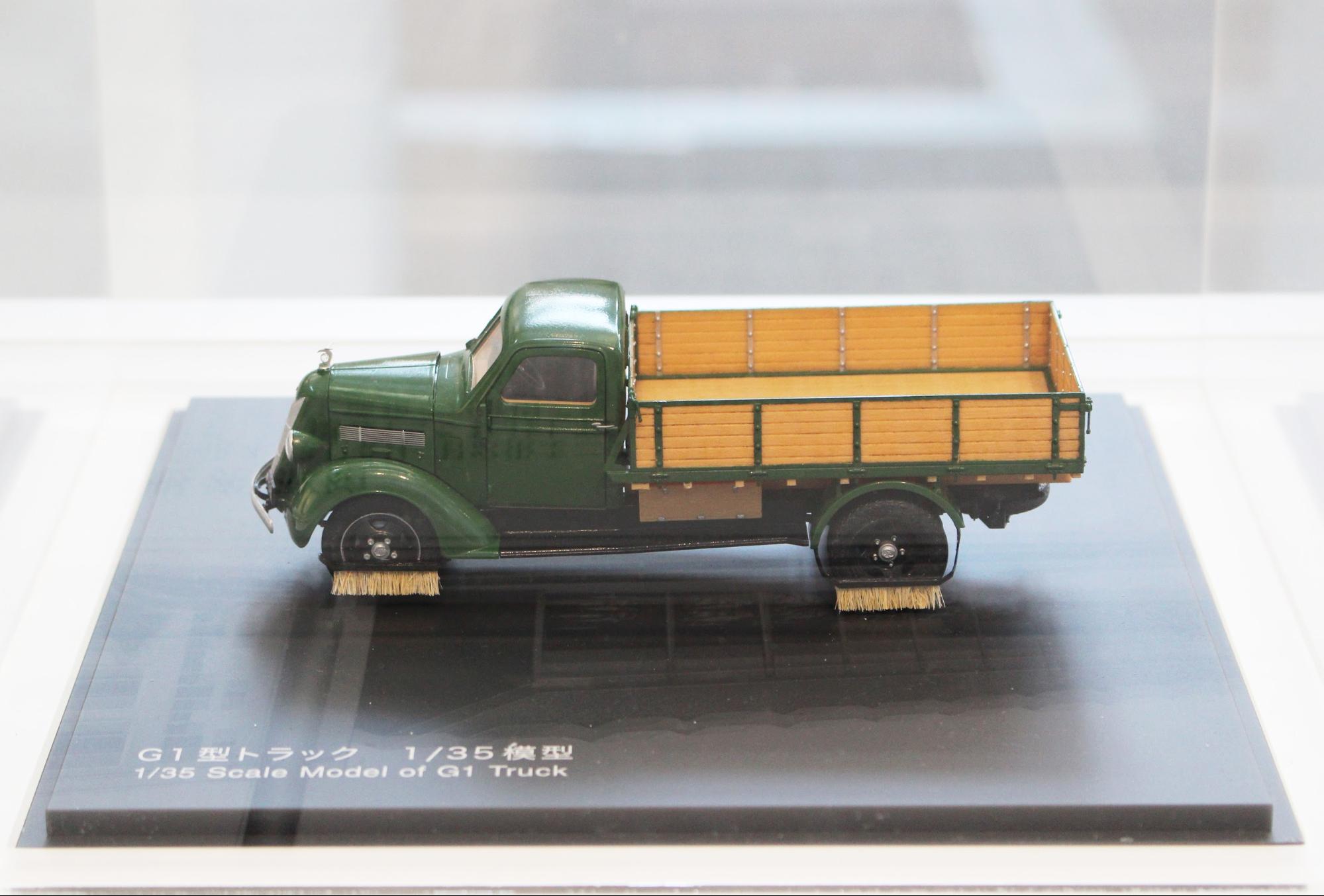
G1型トラック 1/35模型
当時の政府からの要請を受け、喜一郎たちは乗用車の開発を一時中止して急遽トラック製造に着手しました。1935(昭和10)年3月に設計を開始。開発済みのA型エンジンを使用し、製造が間に合わない部品はフォードやシボレーの補給部品を流用。こうして同年8月に「G1型トラック」の試作第1号が完成しました。
しかし、短期間の開発と製造が災いし、「G1型トラック」は故障が続出。不具合箇所一つひとつを改善し、1年間で800件以上の改善を施したことで品質が安定するようになりました。