[Ama City] Learn about the Cloisonne Enamel Ware at "SHIPPO ART VILLAGE"
![[Ama City] Learn about the Cloisonne Enamel Ware at "SHIPPO ART VILLAGE"](https://life-designs.jp/wp/wp-content/uploads/2019/07/image5-2.jpg)
Table of Contents
Cloisonne enamel ware is a traditional craft representative of Ama City, Aichi Prefecture. Cloisonne enamel ware is a piece of metal that is coated with a colorful glass glaze and then fired. SHIPPO ART VILLAGE that we are introducing this time is a facility where you can see, touch, and learn about Cloisonne enamel ware, Cloisonne enamel ware enjoy it as a whole.
You can also make your own original cloisonne enamel ware at the "Cloisonne enamel ware experience class'' inside the facility. This time, I actually tried making cloisonne enamel ware!
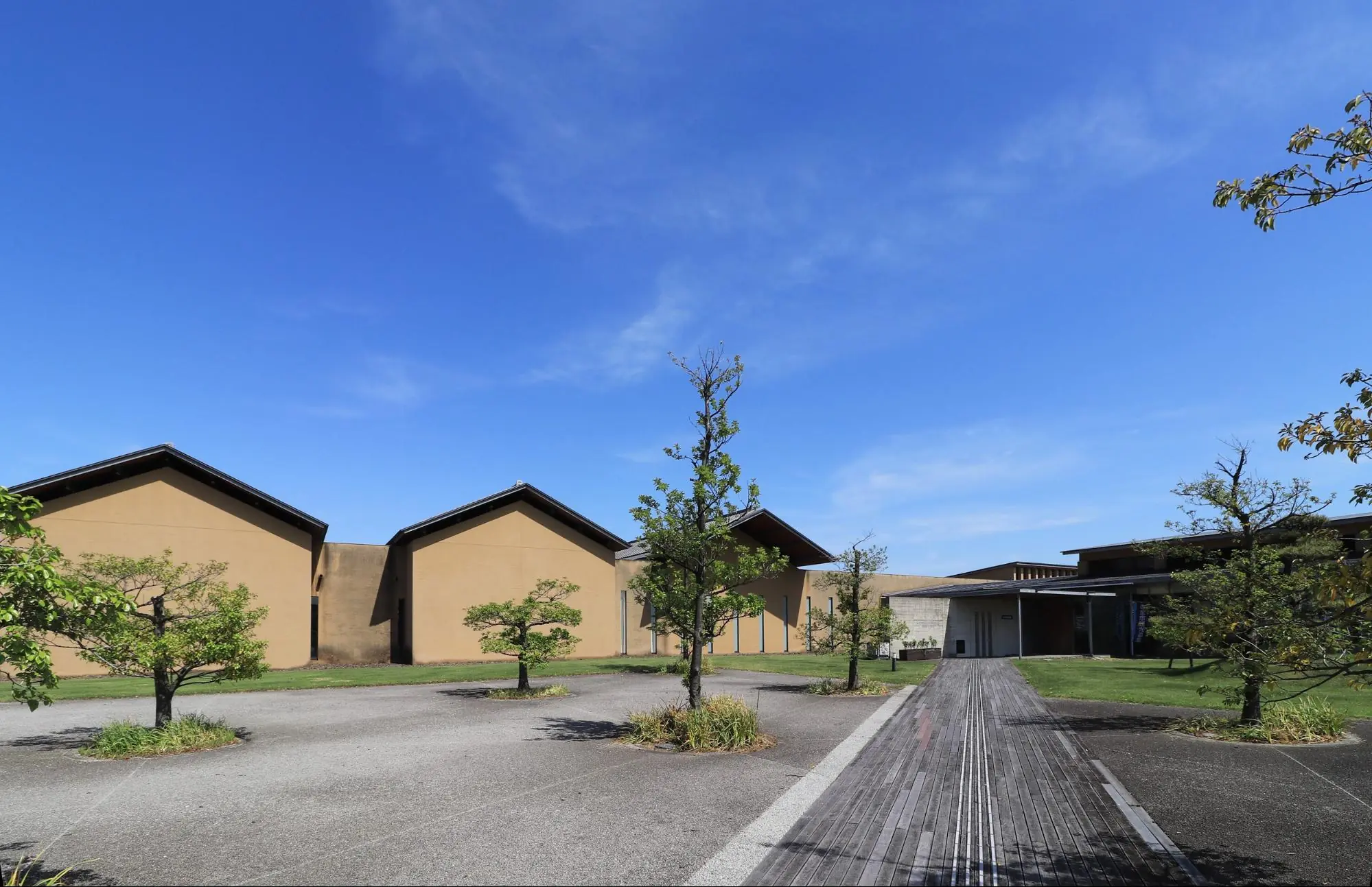
About 20 minutes by car from Nagoya Station
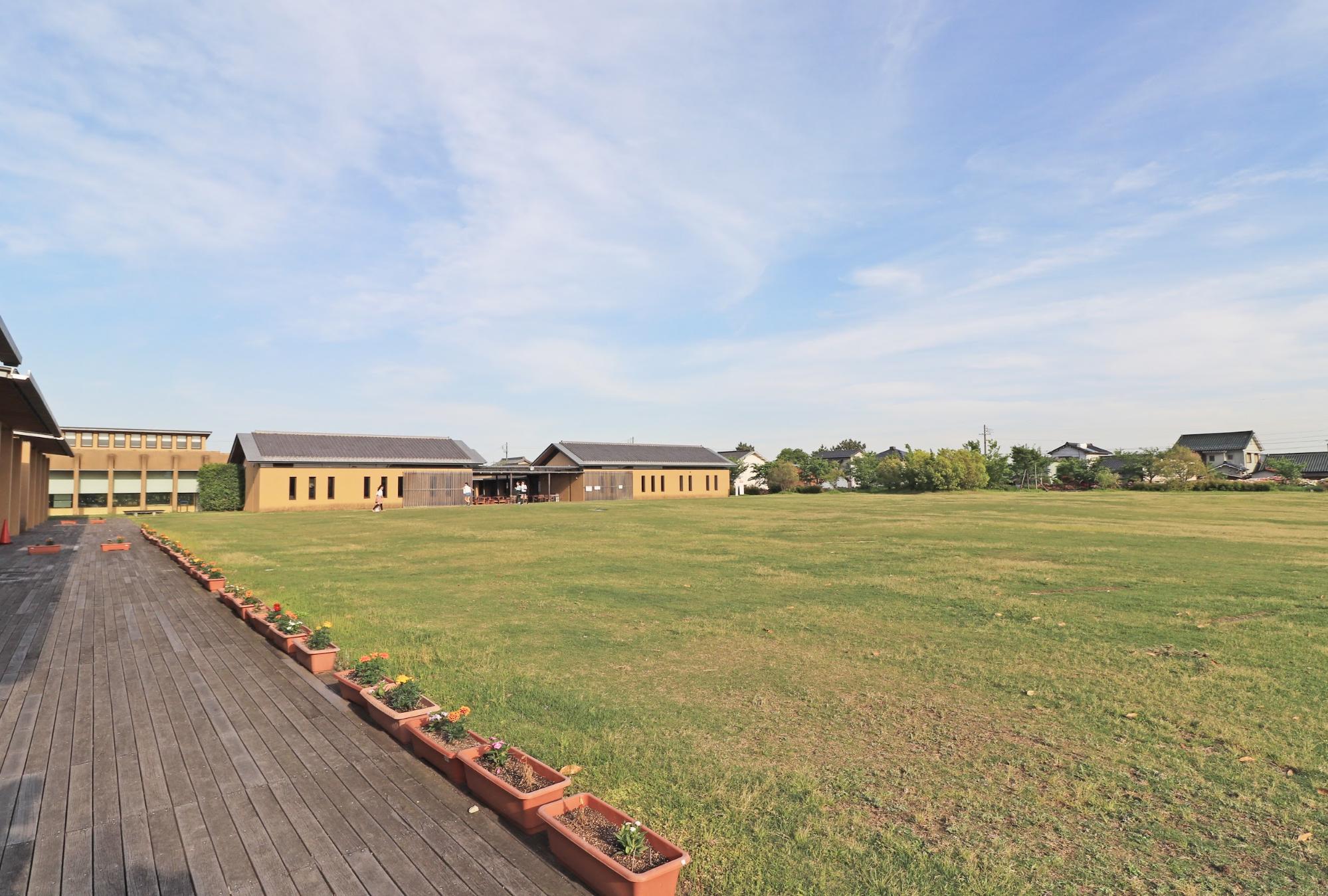
During the weekday evening when I visited Fureai Hiroba (Communication Square), local children were playing.
SHIPPO ART VILLAGE has the "Cloisonne enamel ware Fureai Folklore Museum,'' where you can view cloisonne enamel ware works and observe the production process, and the "Fureai Hitoba, which provides a place for visitors to relax, including walking paths and a plaza.
Cloisonne Enamel Ware Fureai Folklore Museum consists of four areas: an introduction zone, an artwork exhibition zone, a dynamic exhibition zone, and cloisonne enamel ware experience zone. First, let's go to the "Artwork Exhibition Zone" where you can learn about the history of cloisonne enamel ware!
Learn the history and techniques of Cloisonne enamel ware!
"Artwork exhibition zone"
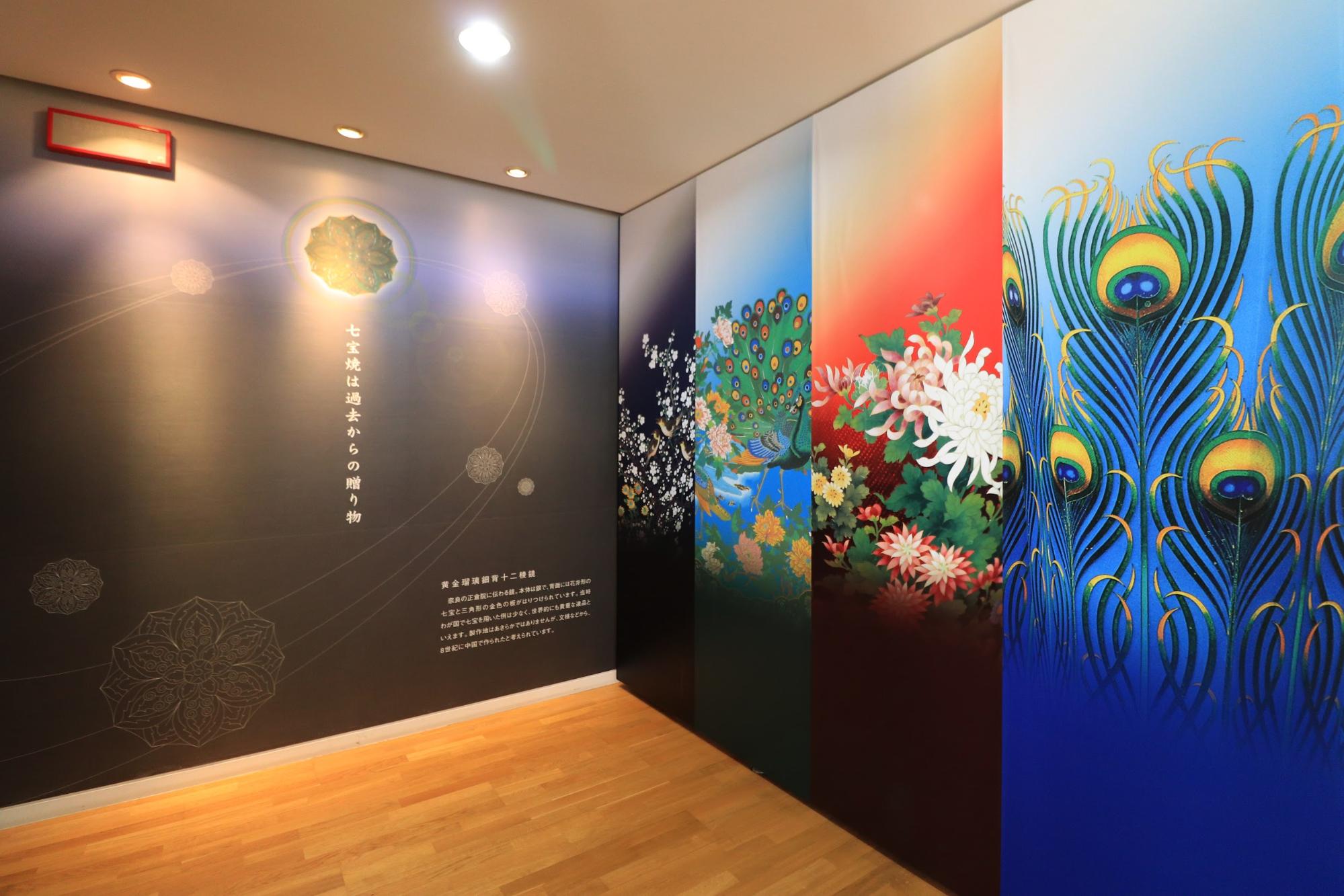
Permanent exhibition entrance
The "Artwork Exhibition Zone" is divided into a permanent exhibition room and a special exhibition room, where masterpieces and tools of Owari Cloisonne, mainly works from the Edo period to the early Showa period, are displayed.
"The Story of Cloisonne ware" History of Owari ware
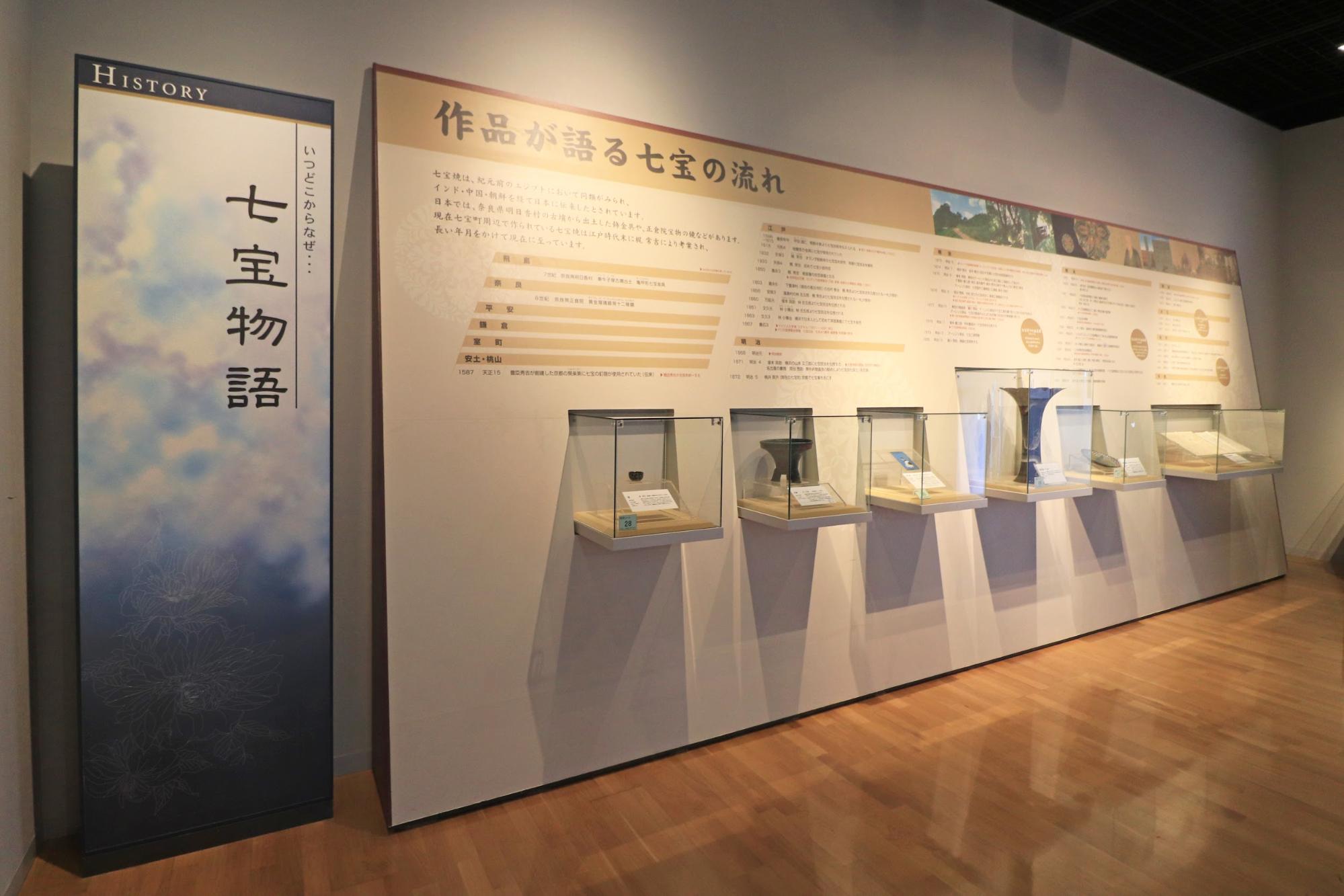
Cloisonne story
The first area of the permanent exhibition introduces the history of cloisonne enamel ware, titled "The Story of cloisonne enamel ware.''
Cloisonne enamel ware ware similar to ancient Mesopotamian civilization and ancient Egyptian civilization can also be found. It is said that this was introduced to Japan via the Silk Road, via China.
Cloisonne enamel ware began to be made in Shippo Town (the name of the area before it merged with Ama City) at the end of the Edo period. It all began in 1833, when Tsunekichi Kaji, who lived in Nagoya at the time, researched Dutch cloisonné plates and discovered how to make cloisonne enamel ware in 1833.
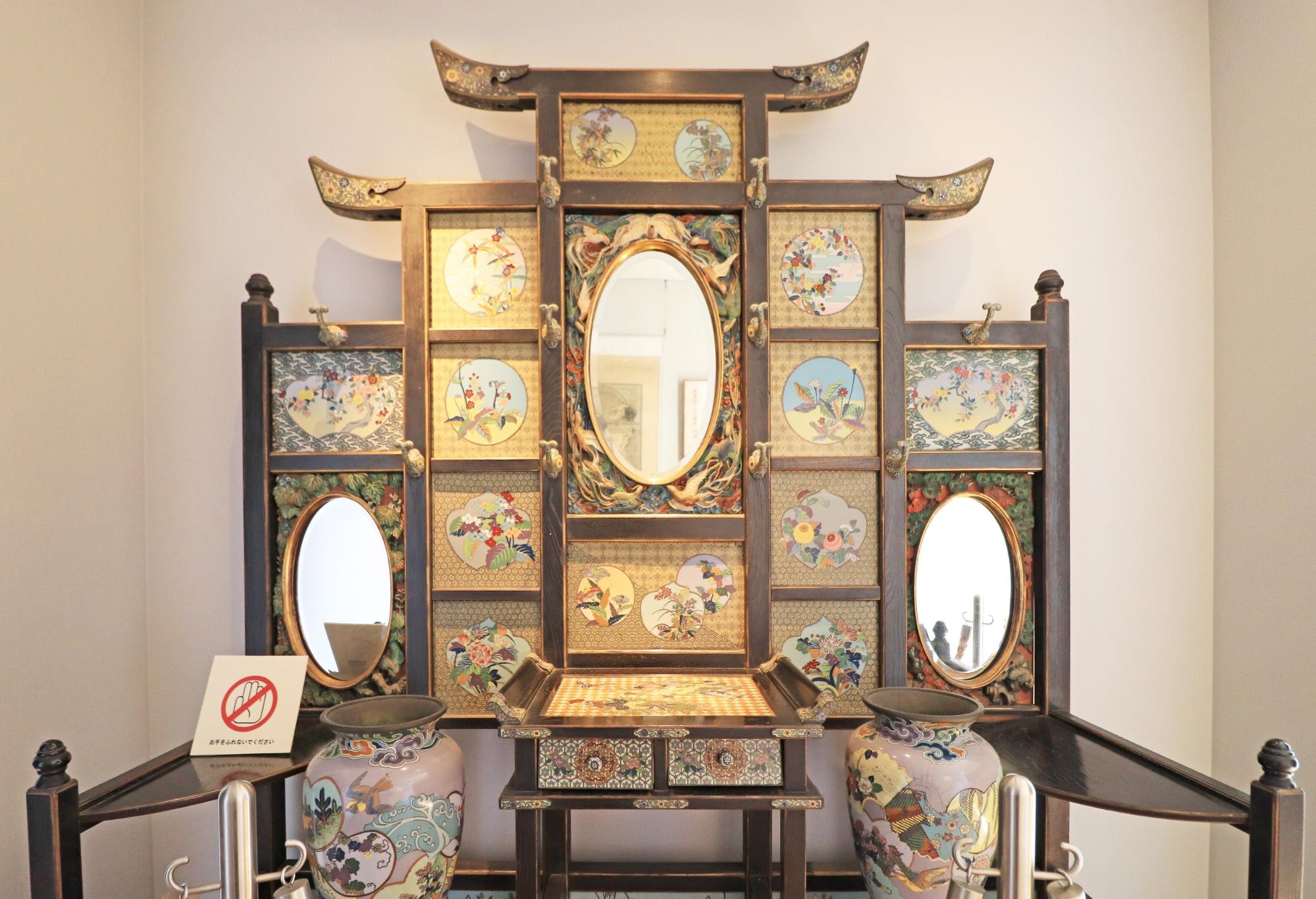
1893 (Meiji 26), "Cloisonne hat rack and vase" made in the Owari region exhibited at the Chicago World Exposition in the United States.
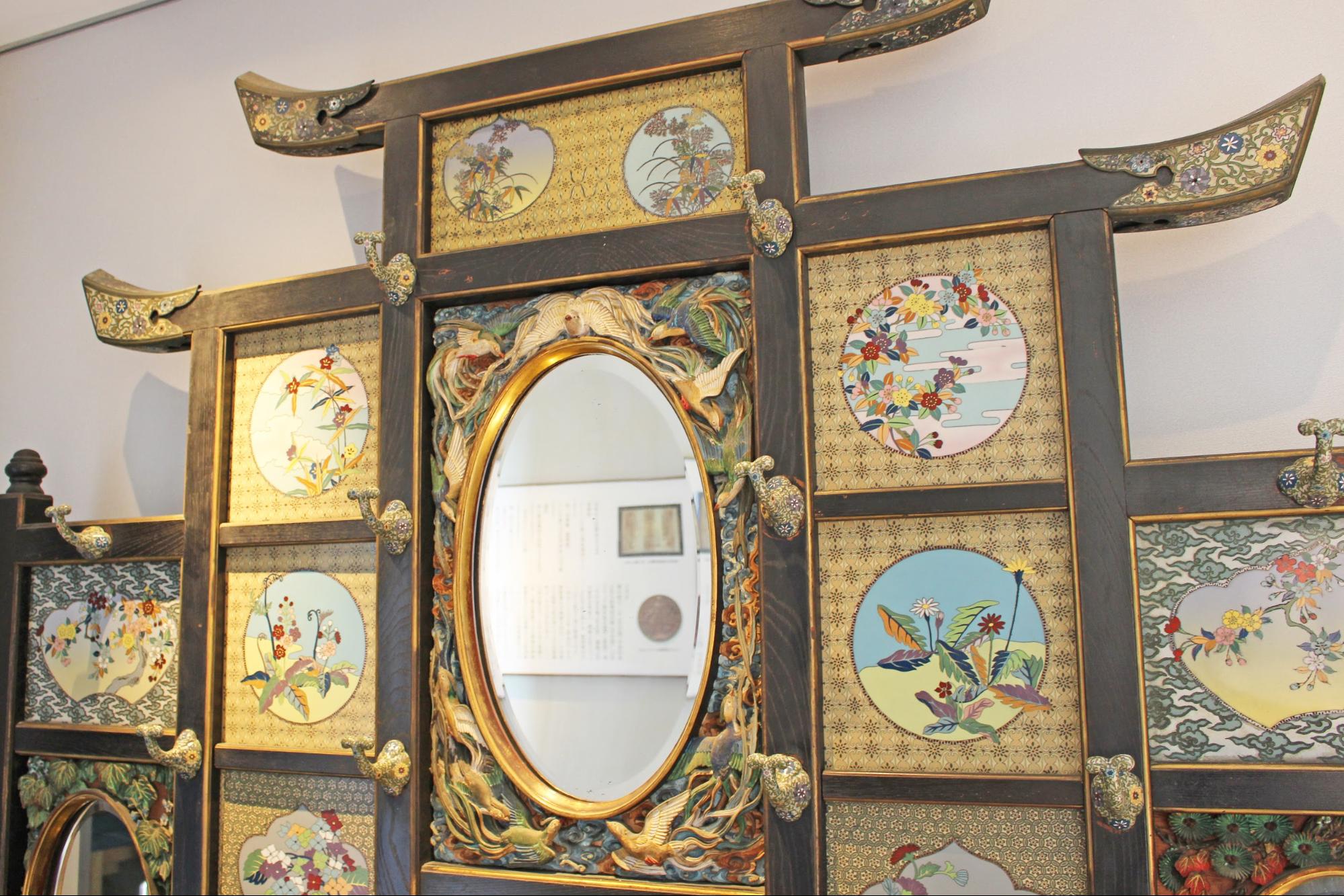
Beautifully detailed decoration!
Cloisonne enamel ware does not require a large kiln. It was a job that could be done even during periods when farm work was idle, so it became popular in this area, where agriculture was the only industry at the time. When it began to be made not only in Shippo Town but also in Nagoya City, the area's Cloisonne enamel ware came to be called "Owari Cloisonne," and at its peak it became a production area with as many as 200 potteries.
“The magic of cloisonne” How cloisonne enamel ware is made
The next area introduces cloisonne enamel ware production process using tools. Cloisonné production is based on a division of labor, with different craftsmen in charge of each process. Even today, there are few parts that can be mechanized, and they are still made by hand based on the years of experience of craftsmen.
Now let's take a look at the process of making Cloisonne enamel ware!
(1) Preparation (making the base)
The base for cloisonne enamel ware is created by pounding a metal plate with a wooden mallet or a hammer. Cloisonne enamel ware looks like pottery at first glance, but you can see that it is based on metal.
②Creating the basics of the composition (painting/edgeline insertion)
A rough sketch is drawn on the surface of the base material with a brush using sumi ink. Metal wire, such as silver or brass wire, is then planted on top of the inked underdrawing to create the outline. This process is called "edgeline insertion".
It is difficult to paint the same pattern over and over again with a brush. Therefore, when making the same pattern in large quantities, stamps for underpainting like this were used.
③ Add color with glaze (glazing)
Next is the process of coloring. Using brushes and "hose" (bamboo spatulas), each color of glaze is applied to the spaces separated by metal wires. The glaze is made by adding water and funori (a paste made from seaweed) to the powdered material.
Once the glaze is applied, it is fired in a kiln. When fired, the glaze melts and becomes glass-like and sticks to the surface, giving it the lustrous finish of cloisonne enamel ware.
④ Repeat until there are no steps (firing)
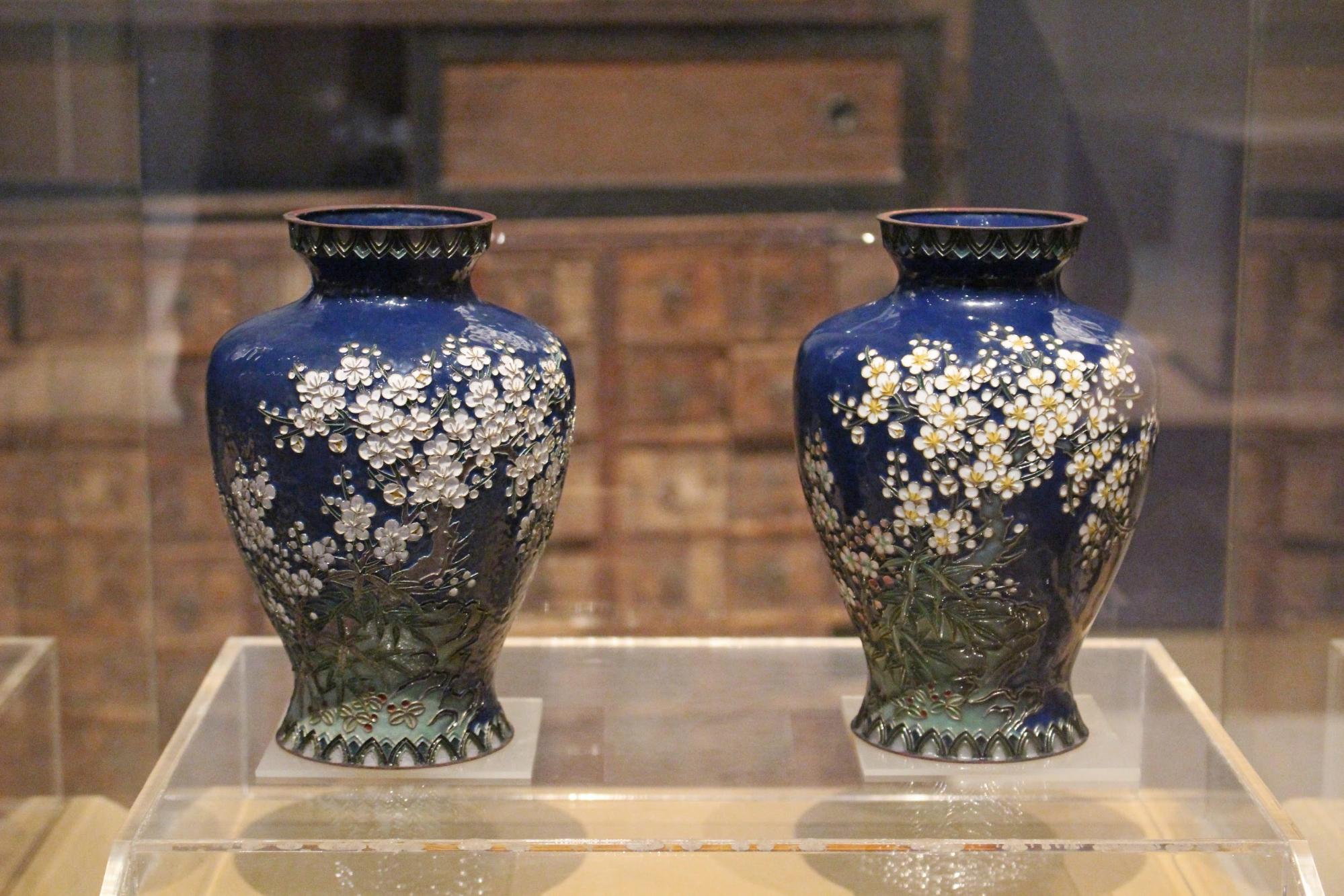
Left: Glazed (first) Right: Glazed (second)
Cloisonne enamel ware is not finished once it is baked.
The process of glazing and firing is repeated three to seven times until there are no more bumps between the metal wire and the glaze. This is a very patient process.
⑤ Final finishing (polishing and attaching a ring)
Left: Polishing Right: Finished
The final touches are polishing and attaching the rings.
First is the polishing. The surface of the fired cloisonne enamel ware is polished to make it smooth and shiny and to show the metal lines clearly.
The next step is to cover the vase. After polishing, the mouth and bottom of the vase are bare metal. Then, silver or silver-plated brass rings are added. This completes the cloisonne enamel ware!
"In Search of Beauty" Introduction of Various Techniques
Here, the technique of cloisonne enamel ware is introduced along with the works.
In modern times, various techniques have been conceived, including those that focus on the planting line and those that focus on the substrate. The trigger was the development of glossy, colorful glazes by the German chemist Mr. Wagener, who came to Japan in the early Meiji period. As a result, the colorful works of art that we see today were produced, and new techniques were invented one after another.
I will introduce some techniques.
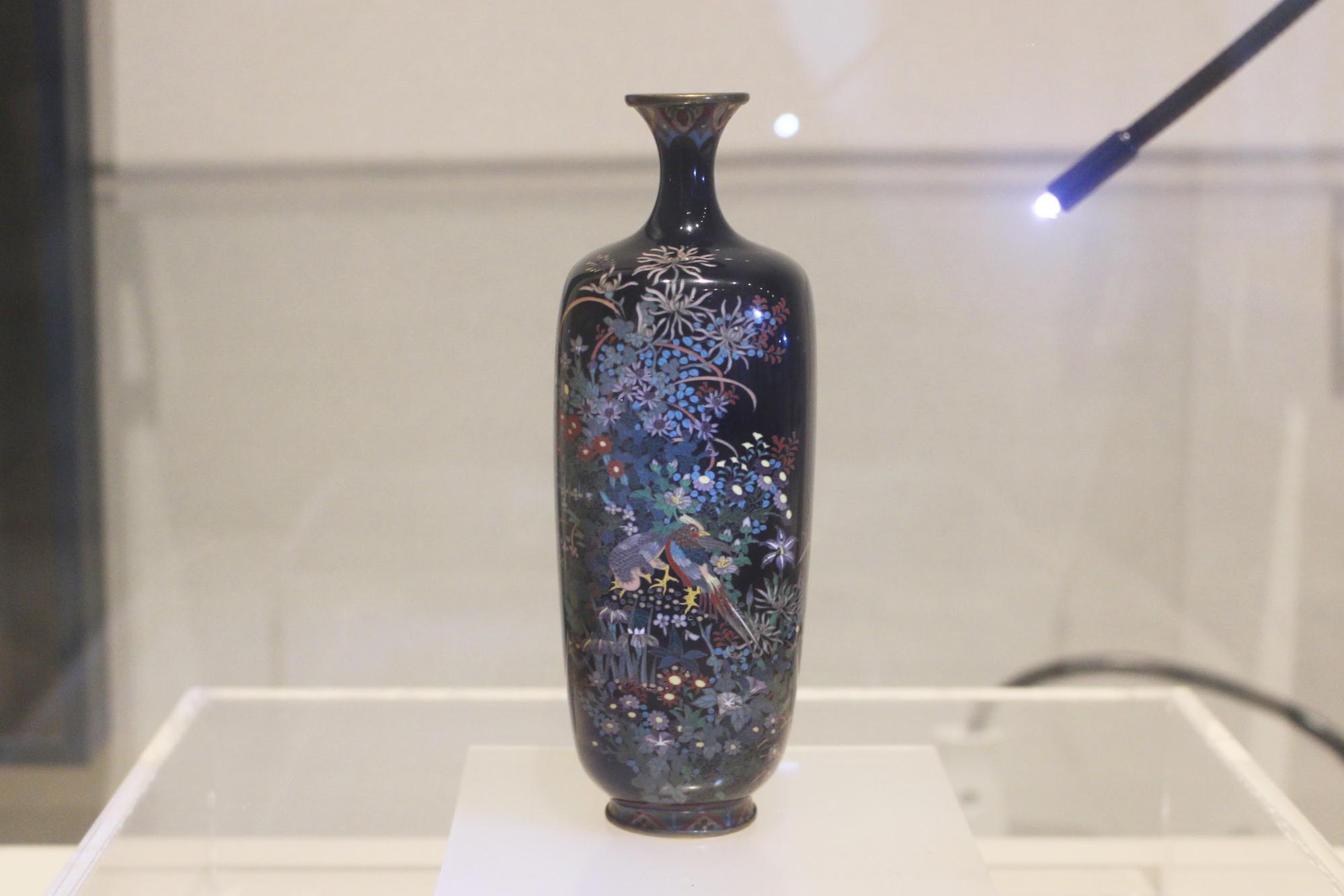
"Mountain, bird, hagi (bush clovers), iris pattern four-sided jar"
For example, in this work, even the details of the design are expressed by planted lines.
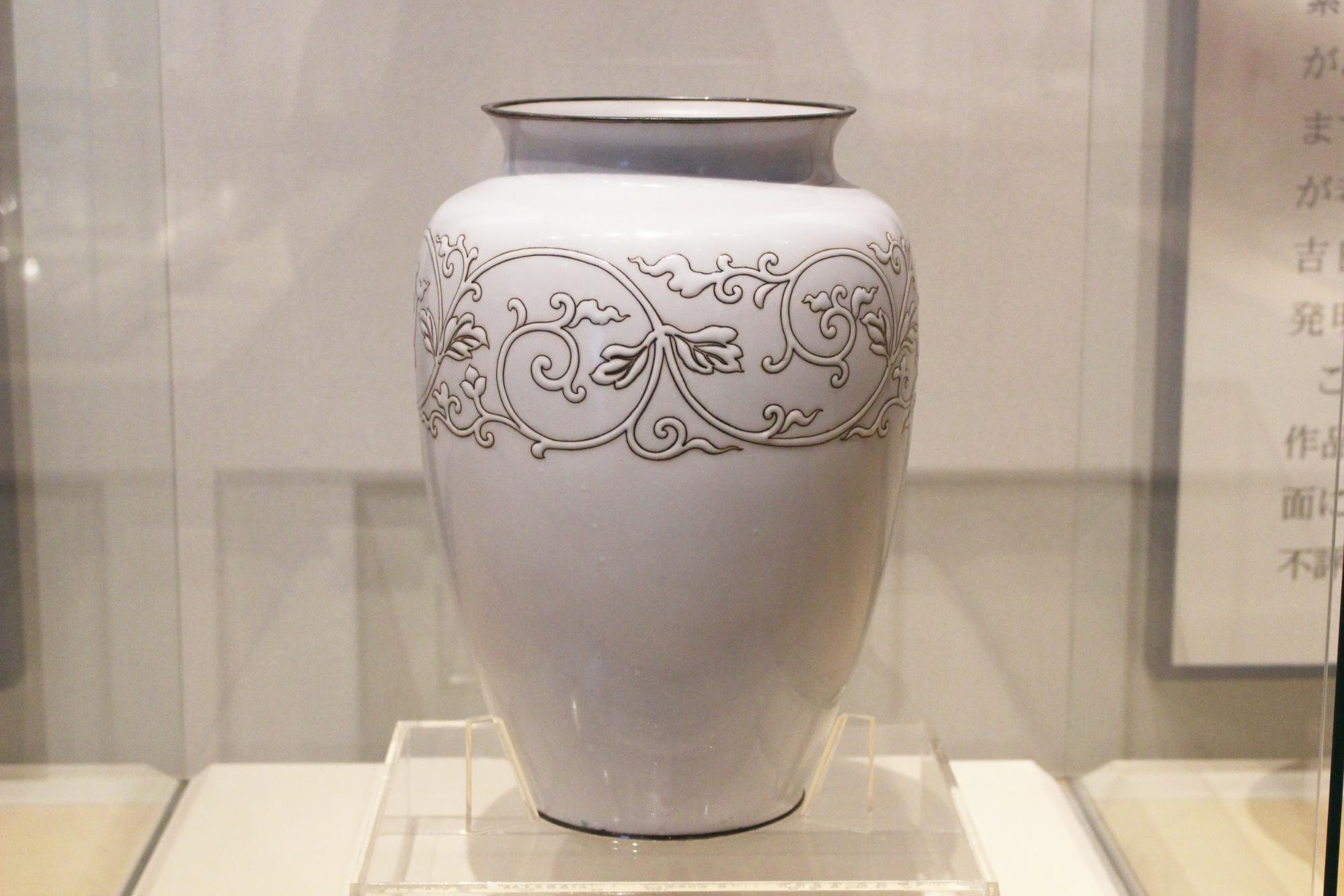
"Morijo Cloisonne Enamel Ware"
Moriage cloisonne is a technique in which glaze is applied only to the parts that you want to raise during the polishing process. The part of the pattern is raised three-dimensionally.
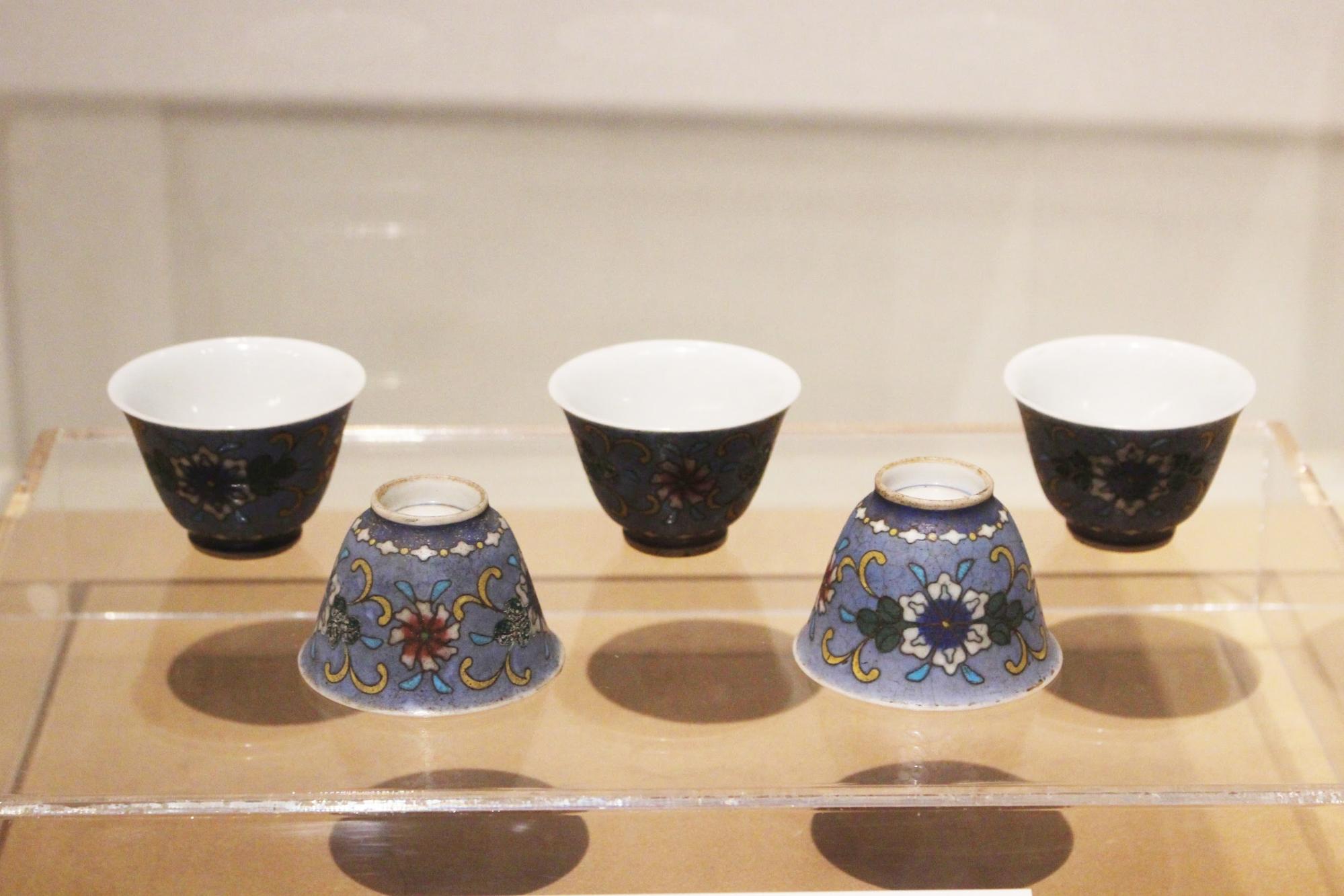
"Ceramic Body Cloisonne Ware Cup 5 Piece Set"
Cloisonne enamel ware generally uses a metal base, but "ceramic cloisonne" uses ceramic or porcelain as the base. This method was widely used in the early Meiji period, but apparently it was no longer produced because the glaze and base did not go well together, causing cracks to form on the surface over time.
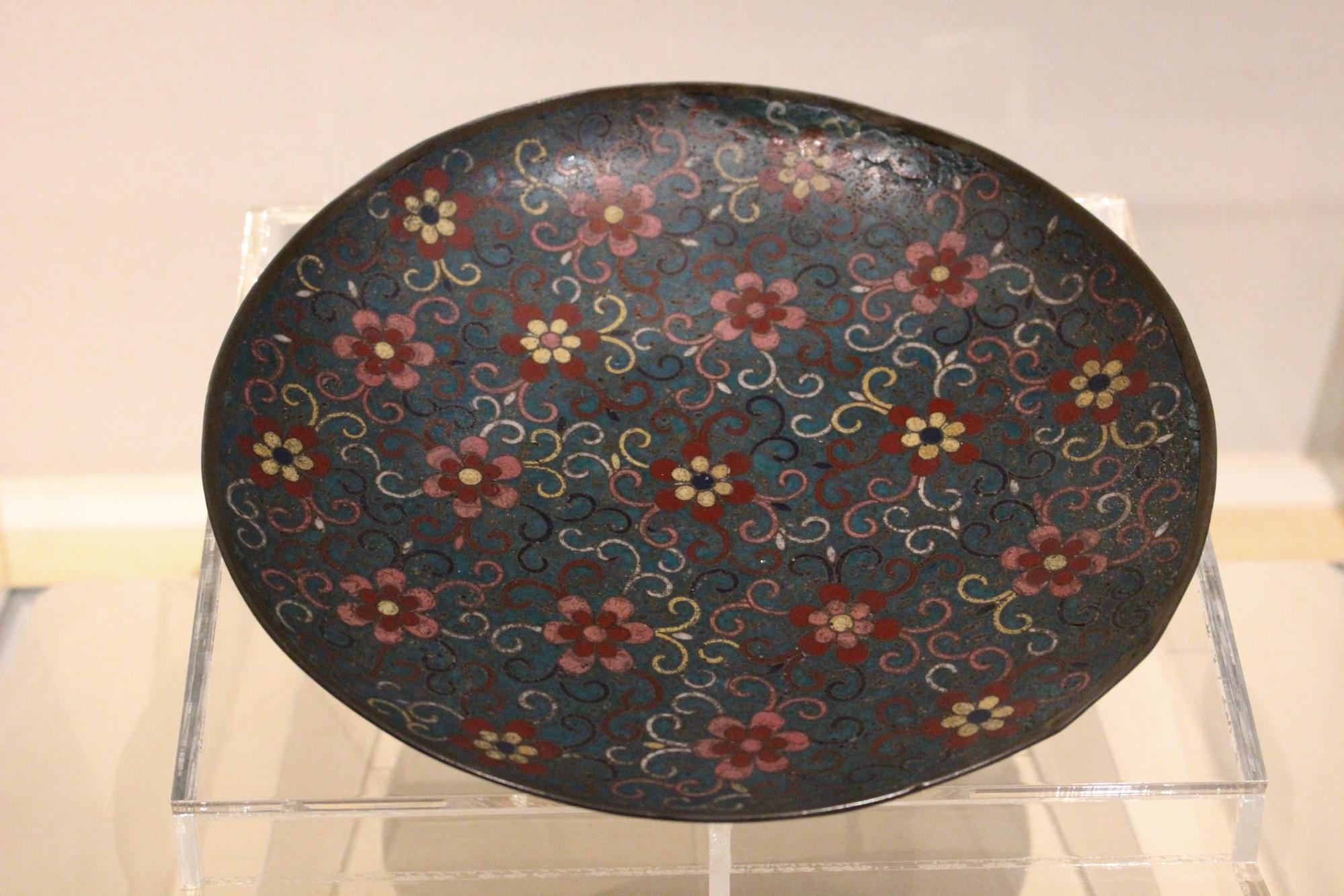
"Flower Pattern Medium Plate"
When you think of cloisonne enamel ware, you think of a glossy finish, but there are also items that don't have that luster. This is "Doro (mud) Cloisonne", a technique that uses a matte and opaque glaze. It is called this name because it has a muddy feel.
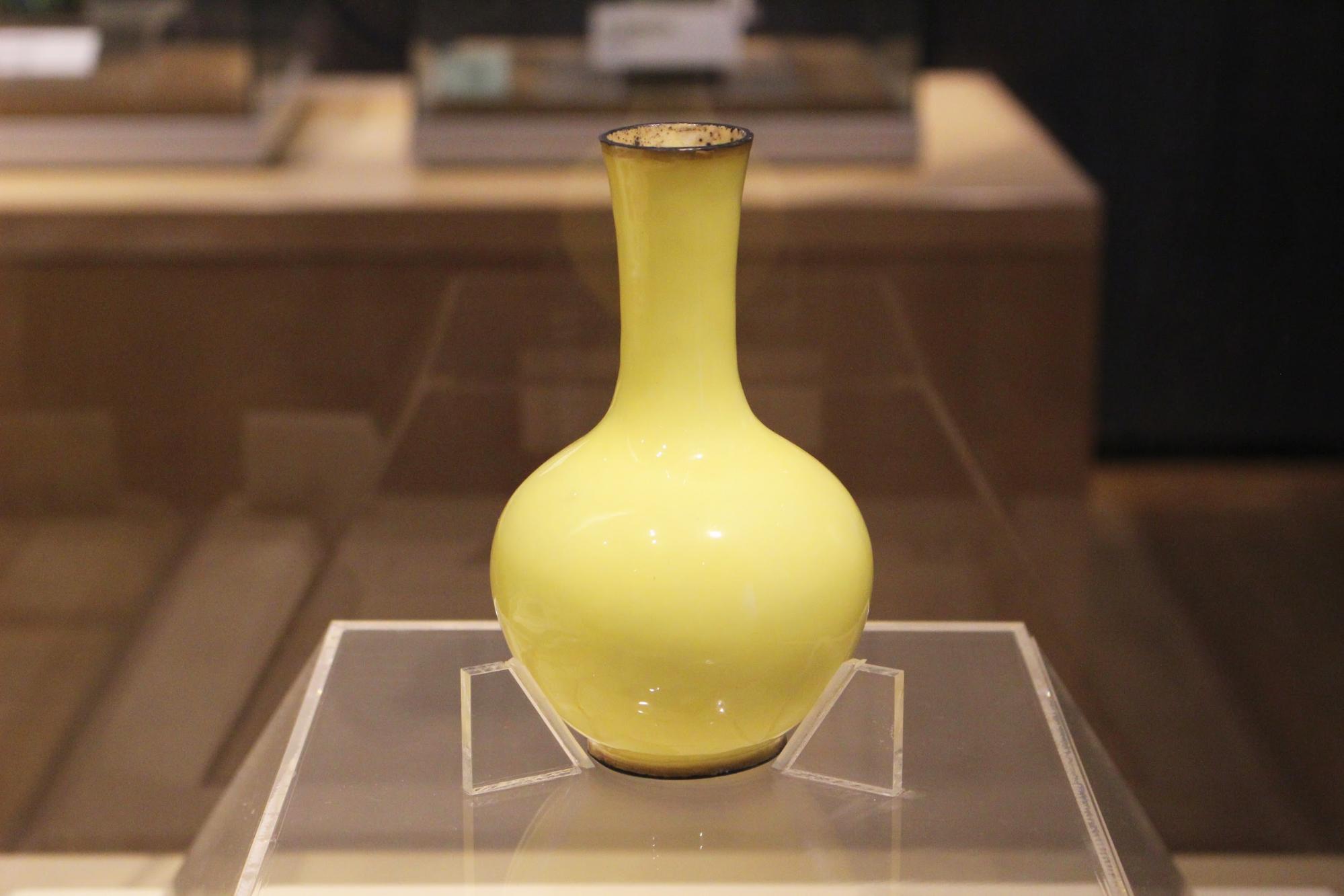
"Silver Background Yellow Pot"
"Silver cloisonne" uses silver as the base material. This ware has a white and bright base, so it is characterized by the good color development of transparent and translucent glazes. It's a very bright color.
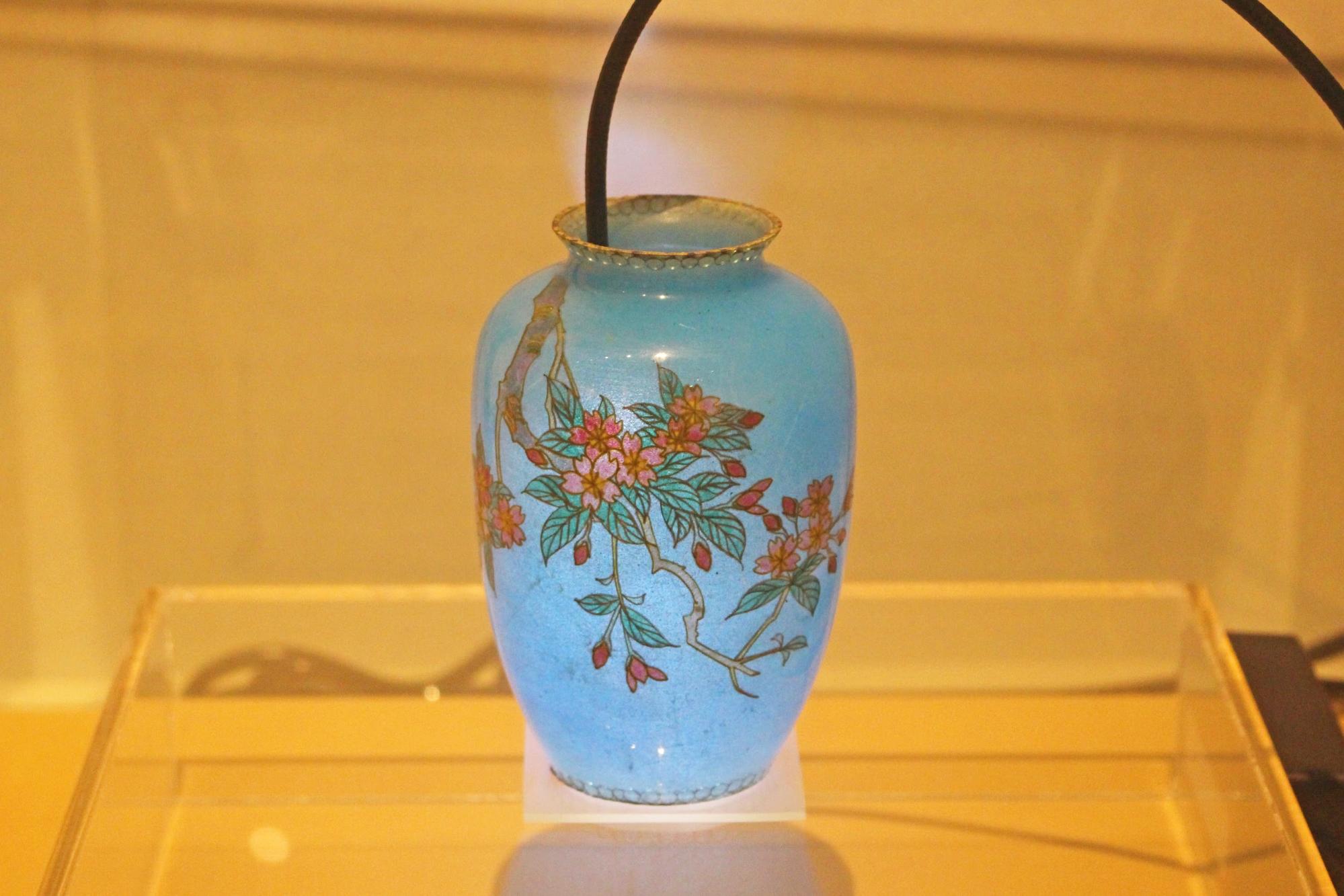
"Shoutai Cloisonne Enamel Ware"
The surface of this vase is transparent.
A technique called "Shotai cloisonne" is used. The copper base is removed by dissolving it with acid, leaving only the silver wire and glaze on the surface. This is a very delicate cloisonne enamel ware made of only 1mm thick silver wire and glaze.
"Craftsmanship" Masterpieces of Owari Cloisonne
In the last area, masterpieces of Owari Cloisonne are introduced. Cloisonne enamel ware is famous for its vases and decorative plates, but it also comes in a variety of other shapes. Cloisonne enamel ware was also made for export overseas. For this reason, it seems that everyday practical items such as matches and cigarette cases were made with cloisonné decorations.