トリップアドバイザーの「工場見学&社会科見学」ランキング1位!トヨタグループの歴史と技術が学べる「トヨタ産業技術記念館」前編
目次
実演で学ぶ!織機技術の発展
続いては、紡機で作られた糸を使って、布ができるまでの工程を実演を通して学んでいきましょう。
佐吉の最初の発明「豊田式木製人力織機」
トヨタグループの創始者・豊田佐吉の最初の発明は、1890年(明治23年)に完成した「豊田式木製人力織機」です。
日本で古くから使われていた「高機(たかばた)」と呼ばれる手織機に、フライシャットル機構を取り付けた「バッタン高機」を改良したもの。開口・よこ入れ・筬打ち(おさうち)の3つの運動を、ペダルの踏み替えと片手で筬柄(おさがら)を前後する動作だけで実現させました。
このシャットルが自動的に左右に移動し、糸を横入れします。
シャットルが飛んでいく様子はついつい見入ってしまいます。熟練の必要がなくなり、織布の生産性がバッタン高機より4~5割ほど向上したのだそう!シンプルな機構ですが、見事なカラクリです。
佐吉の代表作「無停止杼換(ひがえ)式豊田自動織機(G型自動織機)」
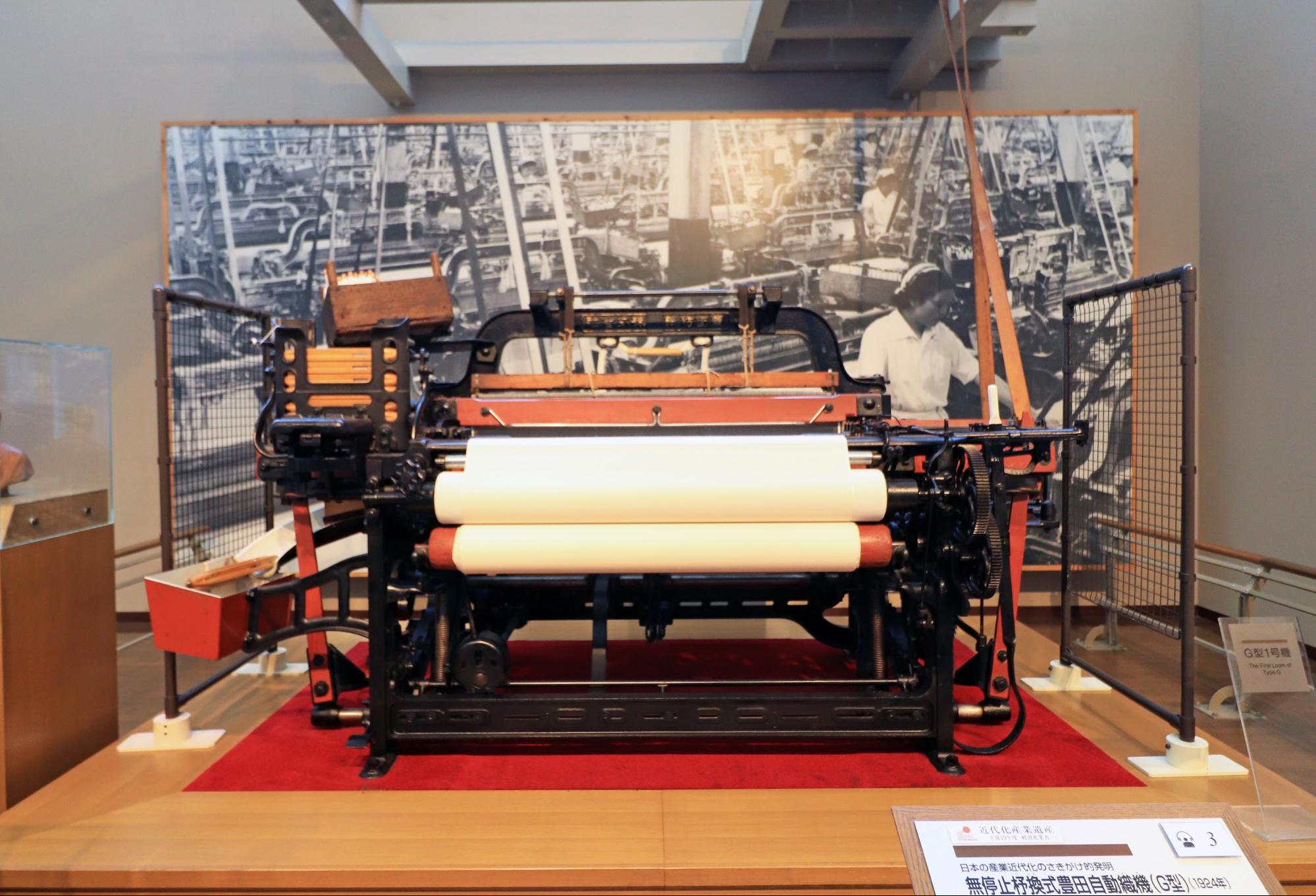
無停止杼換式豊田自動織機(G型)第1号機
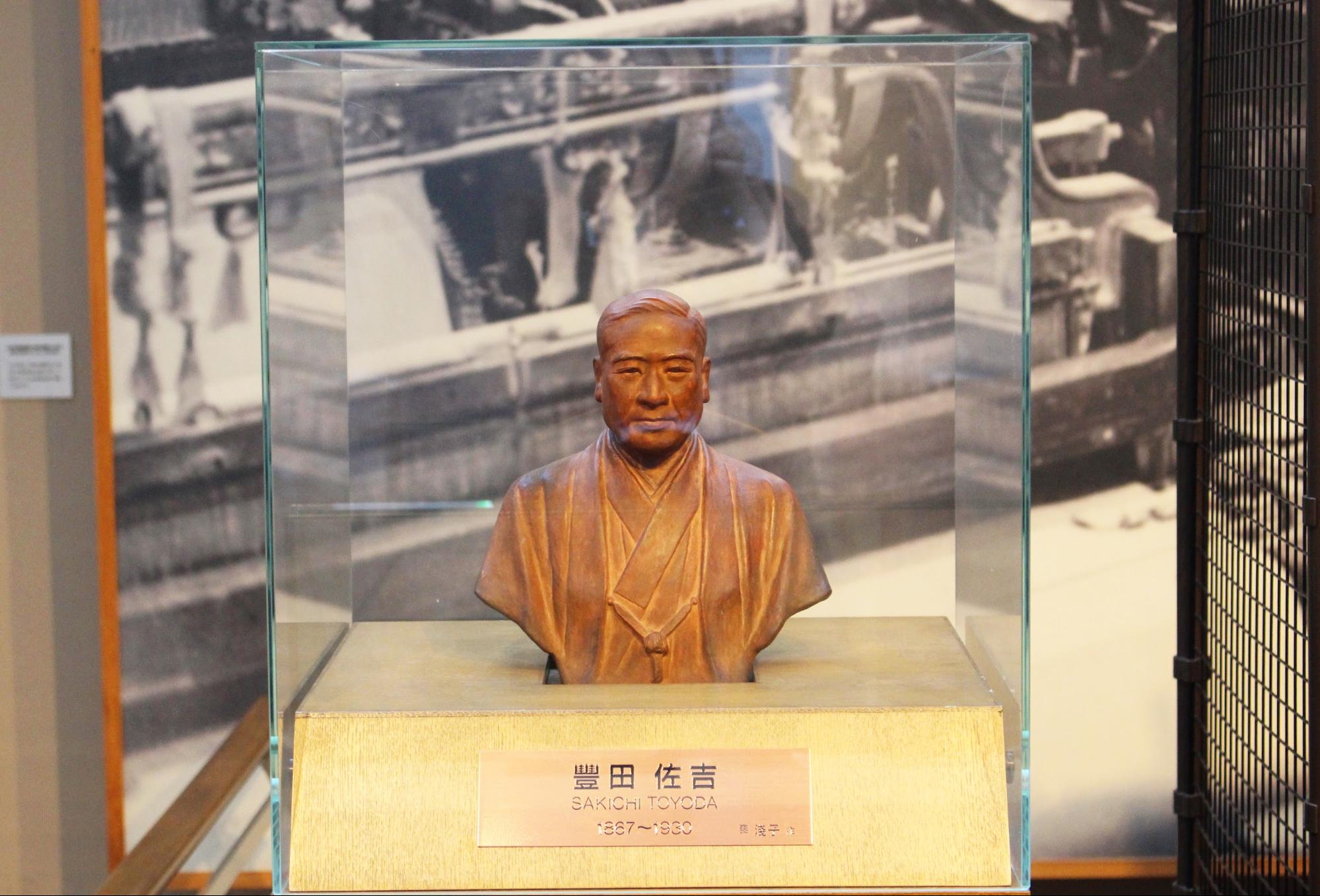
トヨタグループ創始者である豊田佐吉
その後佐吉は、動力織機をはじめ、幅広高速型のN型、着物幅に適したY型など織機を改良し続けました。
そして、佐吉の代表作「無停止杼換式豊田自動織機(G型自動織機)」が完成したのは1924年(大正13年)のこと。このG型自動織機には、佐吉の50余件の発明や考案が反映されています。生産性は大幅に向上し、織物品質も向上し、世界一の性能を発揮。織布業を世界的レベルにまで躍進させるほど日本の産業近代化の先駆けとなりました。
その完成度は「マジックルーム(魔法の織機)」と評されるほどでした。
G型自動織機の登場により、1人の作業者で30〜50台を受け持つことが可能になりました。展示場では、G型自動織機の集団運転も見学できますよ!
生産性向上の切り札は、シャットル(杼)交換の自動化。高速運転中に少しもスピードを落とすことなく円滑に杼(ひ)を交換してよこ糸を補給できます。実際にその様子を見学させていただきましたが、驚くほどの速さでした。
またシャットルにも秘密があります。従来はシャットルに口をつけて糸を通しており、綿ぼこりを吸ってしまうなどの問題があったのだそう。(写真右が従来のもの)
G型自動織機のシャットルは、切れ込み部分に糸をかけ、切れるまで引っ張るとその反動で糸が穴を通る仕組みになっています。こうした小さな工夫の積み重ねによって、効率化をはかっていたのですね。